The magnetron sputtering process involves the use of a magnetron that is placed behind the target material. This magnetron generates a magnetic field that traps electrons near the target surface, leading to a higher ionization rate and a more efficient sputtering process. The resulting plasma is much denser than with traditional sputtering methods, which results in a higher deposition rate and improved film quality.
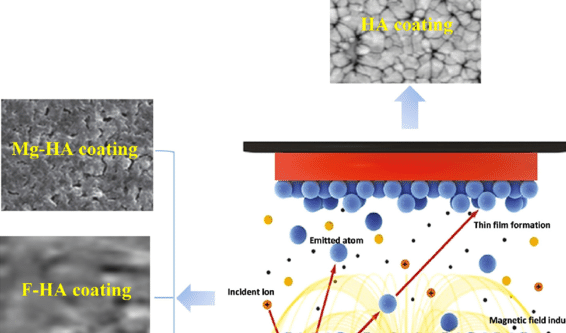
Co-sputtering deposition is a specific type of magnetron sputtering where two or more target materials are used simultaneously to deposit a film with specific properties. This technique is commonly used to create multilayered films, composite films, and alloys. The co-sputtering technique can be used to deposit films with precise control over the composition and thickness of each layer, making it a valuable tool for materials research and development.
One of the main advantages of magnetron sputtering is its ability to deposit uniform films on a wide variety of substrates. Additionally, the ability to use multiple targets allows for precise control over the film composition and properties. Other advantages of magnetron sputtering include relatively low processing temperatures, high deposition rates, and the ability to deposit films with high purity and low defect density.
Overall, magnetron sputtering is a versatile and widely used technique for the deposition of thin films in a variety of industries, including electronics, optics, and biomedical devices. Co-sputtering deposition offers even greater flexibility, allowing for the creation of complex film structures with tailored properties. As technology continues to advance, these techniques are likely to see continued use in materials research and development.