Sputtering machines have revolutionized various industries over the years. They are an essential tool when it comes to various material coatings, and their versatility makes them a valuable asset in many applications.
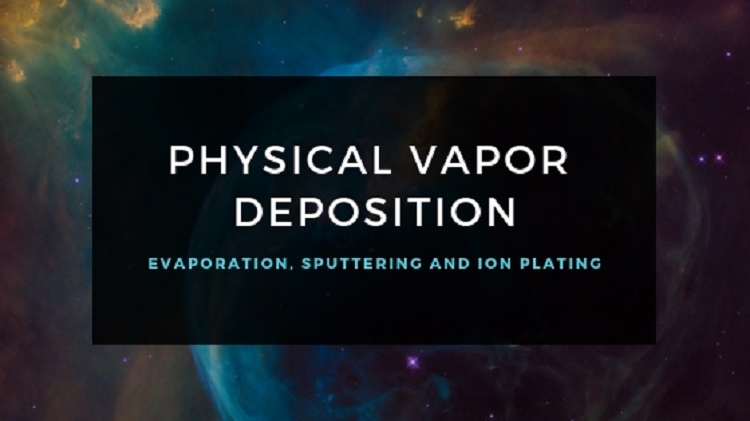
Sputter coaters can lay down thin films of both conductive and insulating material. They use a process known as physical vapor deposition (PVD), which involves the transfer of atoms or molecules from a source material to a substrate. During this process, the target material is bombarded with high-energy ions, which knock atoms or molecules from the surface, causing them to travel in a straight line until they reach the substrate.
The principle of sputtering was first observed in the early 1900s, but it was not until the 1950s that it was used in industry. The first sputtering machine was constructed in the late 1960s, allowing for more precise control and a wider range of materials that could be deposited.
In the years that followed, significant advancements were made in sputtering technology, making it a valuable tool in many industries, including electronics, optics, energy, and more. Today, sputtering machines are used for a wide range of applications, including the production of semiconductors, solar cells, and thin-film magnetic heads for hard drives.
Sputtering machines have also found applications in the automotive industry, where they are used to deposit coatings that reduce friction and wear on engine components. Another area where sputtering has made significant contributions is in the development of advanced thin-film coatings. These coatings offer exceptional protection against wear and tear, corrosion, and oxidation, making them ideal for use in harsh environments.
One of the key benefits of sputtering machines is their ability to deposit the thin films with exceptional precision. This precision is due in part to the fact that sputtering machines are capable of depositing materials at the atomic level, allowing for precise control over the thickness and quality of the coating.
Another benefit of sputtering machines is their ability to deposit coatings onto substrates of varying shapes and sizes. This flexibility makes them ideal for use in a wide range of applications, including the production of complex electronic components, such as microchips and printed circuit boards.
Despite their many benefits, sputtering machines are not without their drawbacks. One of the main limitations of sputtering is its relatively slow deposition rate compared to other coating techniques such as chemical vapor deposition (CVD). However, recent advancements in sputtering technology have helped to mitigate these limitations, allowing for faster and more efficient deposition rates.
Additionally, sputtering machines can be expensive to operate and maintain, which is why they are often used only in higher-end applications where the benefits outweigh the costs.
In conclusion, sputtering machines have made considerable contributions to various industries over the years, providing a highly precise and flexible method for coating materials onto substrates of varying shapes and sizes. As technology advances, it is likely that we will see continued innovation and improvements in sputtering technology, expanding its use to even more applications in the future.